Life Cycle Costing II
- IntelData Pty Ltd | Asset Management and Business
- Feb 4, 2016
- 4 min read
Introduction
As Barringer and Barringer wrote in their paper titled, ‘Life Cycle Cost Summary’ in 2003, Life cycle costs (LCC) are cradle to grave costs summarized as an economics model of evaluating alternatives for equipment and projects. The LCC economic model provides better assessment of long-term cost effectiveness of projects than can be obtained with only first costs decisions.
What is LCC?
According to Society of Automotive Engineers (SAE 1999), Life cycle cost is the total cost of ownership of machinery and equipment, including its cost of acquisition, operation, maintenance, conversion, and/or decommission. The objective of LCC analysis is to choose the most cost effective approach from a series of alternatives (note alternatives is a plural word) to achieve the lowest long-term cost of ownership.
In other words, LCC is an economic model over project life-span. It provides the tools to engineer maintenance budgets, ownership costs, and present decision making scenarios in a financial perspective to achieve the lowest long term cost of ownership (Barringer and Barringer 2003).
LCC and Maintenance
Usually the cost of operation, maintenance, and disposal costs are the major component in the LCC. The use of LCC may help in reduction in the costs of maintenance and operation since these costs are the dominant ones in machinery LCC.
It is one of the tools necessary for effective maintenance control system which can be used to achieve reliable maintenance plans and control procedures.
LCC Estimation Models
Basically, the Life Cycle Cost of a product comprises of two major elements:
Acquisition costs
Sustaining costs
Figure 1 shows the breakdown of these costs.
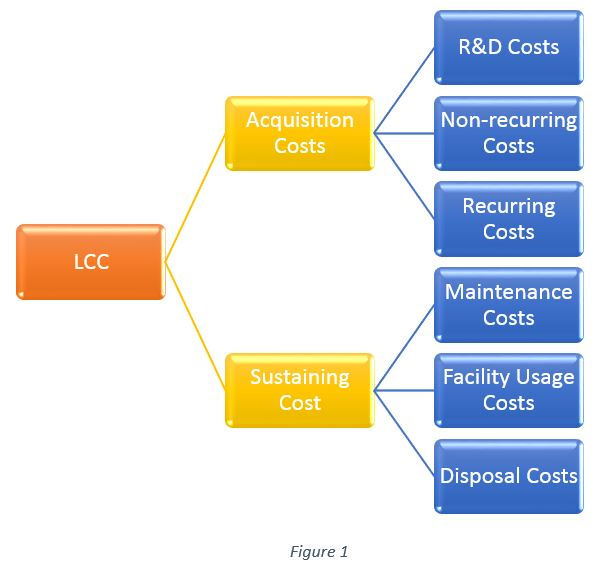
Of course, in many instances there may be other costs involved both in the Acquisition and Sustainment which have be considered.
Based on this basic cost structure, many life cycle cost models have been developed to estimate the life cycle or total cost of a product. They vary in the methods they employ to determine many of the major costs used in the calculation.
According to Dhillon (2006) the followings are the three mathematical models to estimate the life cycle cost of an item.
LCC Model 1
In this model, the life cycle cost (LCC) of a product is assumed to be made up of four major components:
Conceptual Phase Cost (CPC)
Definition Phase Cost (DPC)
Acquisition Phase Cost (APC)
Operational Phase Cost (OPC).
Thus,

Where LCCp is the product, item, or system life cycle cost.
The CPC and DPC are relatively small in comparison to the costs of the acquisition and operational phases. These costs are essentially labour effort costs.
The Acquisition Phase Cost (APC) comprises of the following elements:
Cost of Program Management (CPM)
Cost of Personal Acquisition (CPA)
Cost of the Prime System (CPS)
Cost of Support Equipment (CSE)

The Operational Phase Cost (OPC) is the sum of operational administrative expenses, functional operating expenses, and maintenance costs:

To further breakdown these, we have:
I. Operational Administrative Expense (OAE) which has the following components
spares inventory
investment and holding
administrative costs
operational program management costs
II. Functional Operating Expense (FOE) with the following components:
operational manning
consumables costs
III. Maintenance Cost (MC) which has the following elements:
Cost of repairs and spare parts
Cost of maintenance facilities
Cost of maintenance personnel
Cost of maintenance consumables
Cost of personnel replacement
Cost of equipment downtime
LCC Model 2
This model breaks down system or item life cycle cost into two main components:
1. The recurring cost associated with the system (REC)
2. The nonrecurring cost associated with the system (NREC).
Thus, the system life cycle cost is given by:

Where LCCS is the system life cycle cost.
The NREC is expressed by:

Where NRECi is the ith nonrecurring cost for:
i= 1 (training cost),
i= 2 (acquisition cost),
i= 3 (installation cost),
i= 4 (support cost),
i= 5 (transportation cost),
i= 6 (reliability and maintainability improvement cost),
i= 7 (research and development cost),
i= 8 (life cycle costing management cost),
i= 9 (test equipment cost),
i= 10 (equipment qualification approval cost).
Similarly, the REC is given by

Where RECi is the ith recurring cost for
i= 1 (operating cost),
i= 2 (inventory cost),
i= 3 (support cost),
i= 4 (labour cost), and
i= 5 (maintenance cost)
LCC Model 3
This model was first used by the U.S. Army Material Command to estimate the life cycle costs of new equipment or systems. The equipment life cycle cost is expressed by

Where LCCe is the equipment or system life cycle cost, Crd is the research and development cost, Ci is the investment cost, and Com is the operations and maintenance cost.
The research and development cost, Crd is given by

Where:
C1 is the advanced research and development cost;
C2 is the engineering development and test cost, for example, the cost of engineering models and of testing;
C3 is the engineering data cost;
C4 is the program management cost; and
C5 is the engineering design cost. It includes the costs of reliability, maintainability, system engineering, human factors, electrical design, mechanical design, producibility, and logistic support analysis.
The components of the investment cost, Ci, are as follows:
Construction cost
Manufacturing cost
Initial logistic support cost
The operations and maintenance cost, Com, is given by
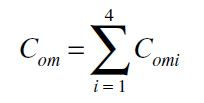
Where:
Com1 is the modification cost;
Com2 is the disposal cost;
Com3 is the operations cost,
Comments