Reliability Management
- IntelData Pty Ltd | Asset Management and Business
- Jan 6, 2016
- 2 min read
Introduction
Reliability management has become an important element of reliability engineering because of various factors including system complexity, sophistication, and size; demanding reliability requirements; and cost and time constraints.
Reliability management is concerned with the direction and control of an organization’s reliability activities such as developing reliability policies and goals, facilitating interactions of reliability manpower with other parts of the organization, and staffing.
General Management Reliability Program Responsibilities
General management plays an important role in the success of a reliability program by fulfilling its responsibilities in an effective manner. Some of its responsibilities are as follows:
Developing appropriate reliability goals.
Providing appropriate funds, manpower, scheduled time, and authority.
Establishing an effective program to fulfil set reliability objectives or goals and eradicating existing shortcomings.
Developing a mechanism for accessing information concerning current reliability performance of the organization with respect to its operations and products.
Monitoring the program regularly and taking appropriate corrective measures with respect to associated policies, procedures, organization, and so on.
A Method for Establishing Reliability Goals and Guidelines for Developing Reliability Programs
When working from pre-established reliability requirements, it is essential to develop appropriate reliability goals. This involves reducing the requirements to a series of sub-goals. The steps of a useful method for establishing reliability goals are shown in Figure 1.
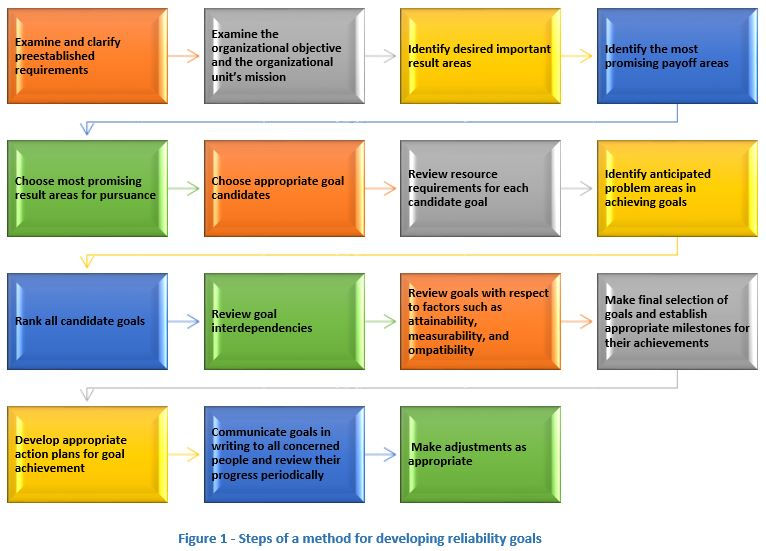
Guidelines for Developing Reliability Program
To develop reliability program Various guidelines have been developed. The followings are the 12 common guidelines found in the realm of reliability engineering for developing reliability program.
Evaluate reliability margins
Develop and maintain control during production through measures such as inspection and sample testing
Establish a closed-loop system for failure reporting, analysis, and feedback to engineering people
Ensure the reporting of the reliability group to an appropriate authority
Develop a testing program
Establish an on-the-job training facility and program
Conduct specification review
Review reliability-related changes in specification and drawings
Assign responsibility for reliability to a single group
Put maximum effort during the design phase to achieve maximum “inherent equipment reliability”
Conduct procedure and design reviews
Assign reliability goals for system under consideration
References
Dhillon, B. S. (2006). Maintainability, Maintenance, and Reliability for Engineers. Taylor & Francis Group.
NASA. (2000). Reliability Centered Maintenance Guide for Facilities and Collateral Equipment. National Aeronautics and Space Administration.
Yorumlar