Reliability Management Tools and Documents
- IntelData Pty Ltd | Asset Management and Business
- Jan 11, 2016
- 3 min read
Reliability management uses a variety of tools and documents. Some examples of these tools are:
Configuration management
Value engineering
Critical path method.
Similarly, some of the documents used by reliability management are the reliability manual, international and national specifications and standards, policy and procedure documents, plans and instructions, and reports and drawings.
Some of the above items are discussed below.
Configuration Management
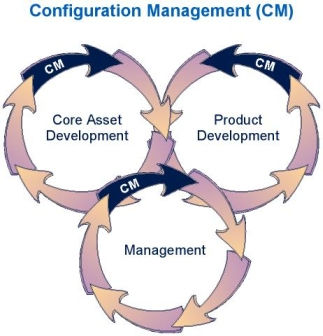
During the development of an engineering system or product many changes may occur; these changes may be concerned with product performance, weight, size, appearance, and so on. Configuration management is a useful tool to assure the customer and the manufacturer that the end product will fully satisfy the contract specification. Thus, configuration management is the management of engineering requirements that define the engineering product or system as well as changes to it.
The history of configuration management can be traced back to 1962, when the U.S. Air Force released a document entitled “Configuration Management During the Development and Acquisition Phases,” AFSCM 375-1. Today configuration management is well known in the industrial sector, and its advantages include:
Reduction in overall cost
Effective channelling of resources
facilitation of accurate data retrieval
elimination of redundant efforts
formal establishment of objectives
precisely identified final product.
Value Engineering
Value engineering is a systematic, creative technique used to accomplish a necessary function at the minimum cost. The financial returns from the application of this concept are very promising (somewhere between $15 and $30 for each dollar spent).
The history of the value engineering concept can be traced back to 1947, when General Electric Company assigned Lawrence D. Miles a project to develop methods for reducing costs through material substitution or changes in design or production methods.
Value engineering is useful in many areas including:

Identifying areas requiring attention and improvement
Prioritizing
Increasing the value of goods and services
Generating new ideas to solve problems.
It also serves as a useful tool to determine alternative solutions to a concern, a useful procedure for assigning dollars on high-value items, a means to document rationales behind decisions, and a useful approach for determining and quantifying intangibles.
Critical Path Method
The critical path method (CPM) along with the program evaluation and review technique (PERT) is widely used for planning and controlling projects. It was developed by E.I. DuPont de Nemours and Company in 1956 for scheduling design- and construction-related activities.
The following general steps are associated with this method:

Break down the project under consideration into individual tasks or jobs.
Arrange the jobs or tasks into a logical network.
Estimate the duration time of each task or job.
Develop a schedule.
Highlight jobs or tasks that control the completion of the project.
Redistribute resources and funds to improve the schedule.
Some of the advantages of the CPM are that it is useful to determine project duration systematically, show interrelationships in work flow, improve communication and understanding, identify critical work activities for completing the project on time, monitor project progress effectively, and determine the need for labour and resources in advance. It is also useful in cost control and cost saving.
Reliability Manual
This is the backbone of any reliability organization. Its existence is absolutely necessary for any organization irrespective of its size. A typical reliability manual covers topics such as the followings:

Company-wide reliability policy
Organizational structure and responsibilities
Relationship with suppliers and customers
Product design phase procedures from the standpoint of reliability
Effective reliability methods, models, etc.
Reliability test and demonstration approaches and procedures
Failure data collection and analysis methods and procedures to be followed
Comentários